High Rigidity Portal Milling Machining Center
Technical Specifications
Model |
Unit |
SKH2016 |
SKH2500 |
SKH3020 |
SKH4025 |
Travel |
|
|
|||
X Axis |
Mm |
2,200 |
2,700 |
3,200 |
4,200 |
Y Axis |
Mm |
1,600 / 2,000/2500/3000 |
|||
Z Axis |
Mm |
800(1,000-Opt.) |
|||
Distance From Spindle Nose To Table |
Mm |
150 - 950(150 / 1,150-Opt.) |
|||
Distance Between Two Column |
Mm |
1,700 / 2,100/2600 |
|||
Working Table |
|
|
|||
Table Length |
Mm |
2,000 |
2,500 |
3,000 |
4,000 |
Table Width |
Mm |
1,600 / 2,000 |
|||
Table Load |
Kg |
6,000 |
7,000 |
9,000 |
10,000 |
T- Slot (Width X Number X Pitch) |
Mm |
22x7x180 / 22x9x180 |
|||
Spindle |
|
|
|||
Spindle Taper |
- |
BT-50 / ISO-50 / CAT-50 |
|||
Spindle Speed |
Rpm |
3,000(6,000-Opt.) |
|||
Spindle Motor(Cont./30 Minutes Rated) |
Kw |
18.5 / 22 (22/26-Opt.) |
|||
Feed |
|
|
|||
Rapid Traverse(X/Y/Z) |
M/Min |
12 / 12 / 15 |
10 / 12 / 15 |
||
Cutting Feedrate |
Mm/Min |
7,000 |
|||
Accuracy |
|
|
|||
Positioning Accuracy |
Mm |
±0.005 / 300 ; ±0.015 / Full Travel |
|||
Mm |
P0.03 |
P0.035 |
|||
Repeatability |
Mm |
±0.003 |
|||
Mm |
0.025 |
0.028 |
|||
ATC |
|
|
|||
Tool Magazine Capacity |
Pcs |
32 (24/40/60-Opt.) |
|||
Max. Tool Size (Full Pocket/Next Pockets Empty) |
Mm |
Ø125/245 |
|||
Max. Tool Length |
Mm |
350 |
|||
Max. Tool Weight |
Kg |
20 |
|||
Others |
|
|
|||
Power Required |
Kva |
65 |
|||
Pneumatic Input Pressure |
Kg/Cm2 |
6.5 |
|||
Machine Net Weight |
Tons |
20 / 22 |
22 / 24 |
24 / 26 |
28 / 30 |
Floor Space (LxWxH) |
M |
8.5x5.1(5.5)X4.7 |
10.5x5.1(5.5)X4.7 |
12.5x5.1(5.5)X4.7 |
15.2x5.1(5.5)X4.7 |
Machine Configuration
Automatic Lubrication System |
Spindle Oil Cooler |
Air Blast Through Spindle |
Manual Pulse Generator |
Working Lamp |
3-Color Alarm Lamp |
RS-232 Interface |
Heat Exchanger For Electrical Cabinet |
Water Gun And Air Gun Interface |
Cutting Coolant System |
Twin Auger Chip Removal System |
Belt Type Chip Conveyor With Cart |
X Axis Heidenhain Linear Scale |
Sub-Table |
3 Axes Manual Pulse Generator For Mold Processing |
Coolant Through Spindle At 20/40/70 Bar |
Coolant Through Tool Holder Interface |
Air Conditioner For Electrical Cabinet |
Transformer |
Oil Skimmer |
Oil Mist Collector |
Picture Display
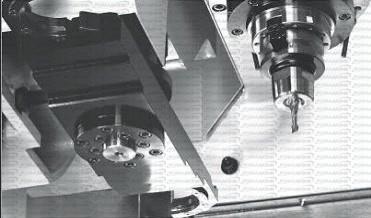
Automatic Tool Change System
Fast and safe tool-changing system provides quick balancing and reliable tool-exchanging action controlled by PLC. The tool-exchanging time is about 8 seconds, which reduces the non-cutting time.
Rotating control box
Rotating seat-type operation control panel and portable handwheel box are very convenient for the operator to use anywhere. Foot switch can easily clamp and loosen the tool on the secondary spindle head.
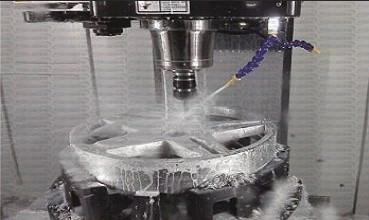
Quality Details
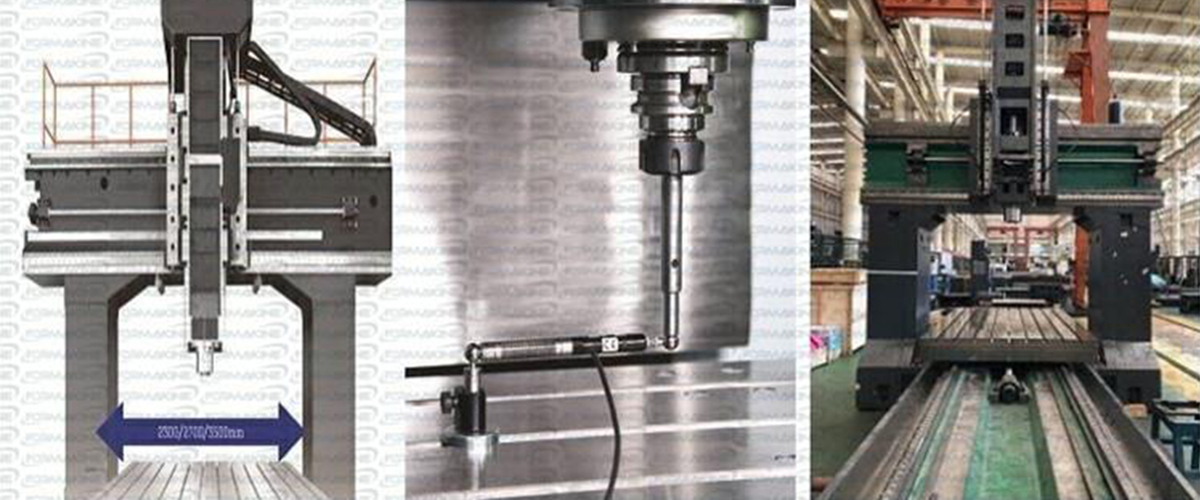
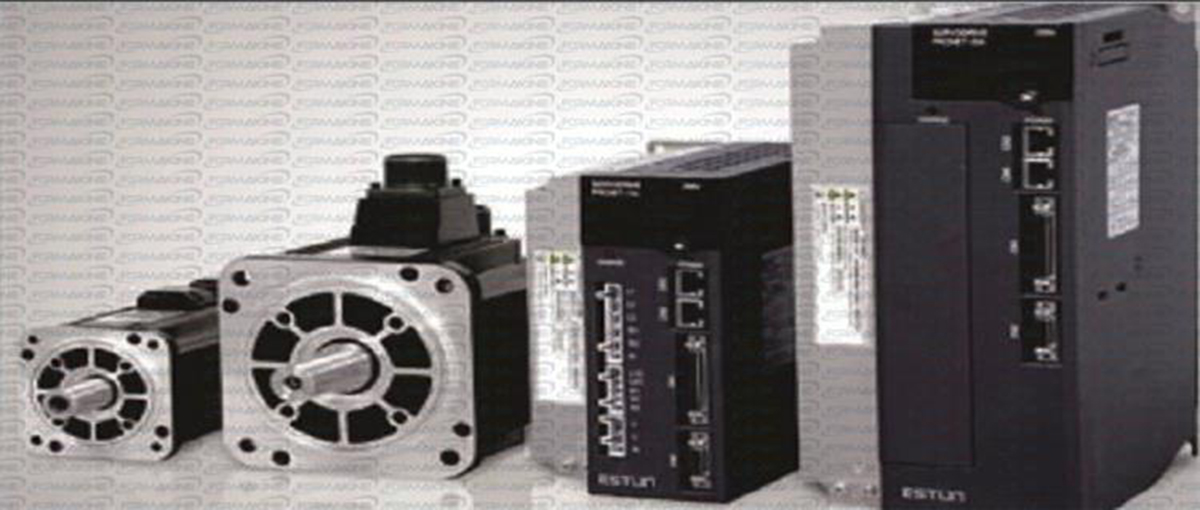
Axis Servomotor
The servo motor drives the screw rod directly through the coupling, which has less vibration and higher precision. The three-axis servo motor has built-in absolute encoder to measure displacement indirectly and form a semi-closed-loop system to ensure the positioning accuracy. The three-axis positioning is set by the numerical control system.
Packing & Shipping
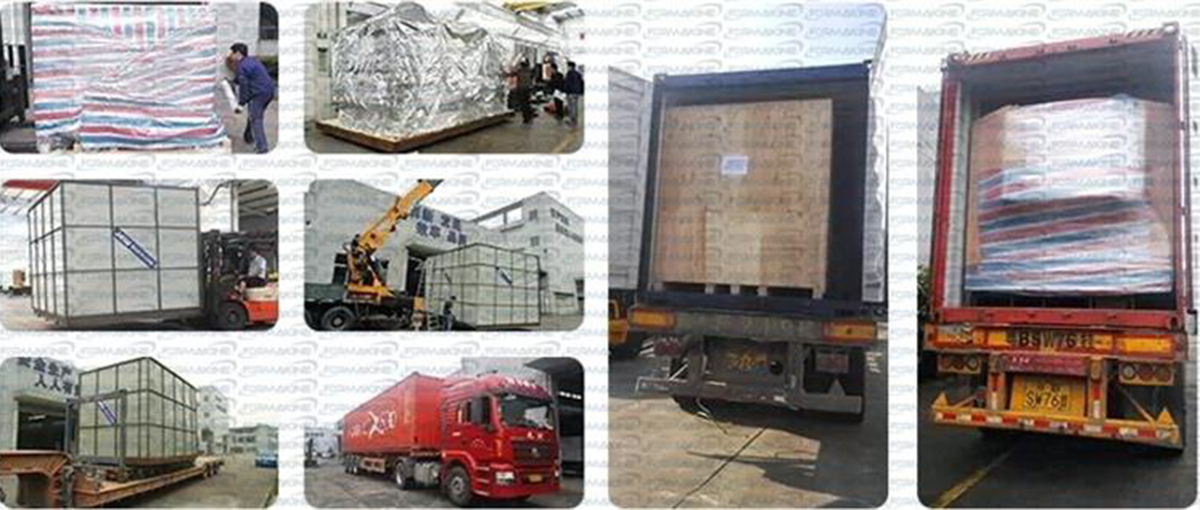