H Frame Air Conditioner High Speed Aluminum Press
Product Details
100 Ton Four Uprights Two Points High Speed Fin Press Machine
Stroke Of Slide: 40mm
Die Height Adjustment: 50mm
Slide Lifting Height (At Min Die. Height): 120mm
Die Height: 270-320mm ( Fulfill The Die Setting Requirements )
Size Of Table: 1200x1800( Fulfill The Die Setting Requirements )
Bottom Size Of Slide: 1190x1300mm
Feed Exchange Structure, Feeding Length: 0-120mm
With Air Feeder
Fin Parameter: Φ9.52×25×21.65×36R×2P ( The Buyer Supply The Drawing)
With Scrap Case
With Oil –Spraying Unit
Fin Press Specification |
|
Type | FMC-36A-100, High speed Fin precision Straight Side press |
Capacity | 1000KN |
Working efficiency | No-load stamping frequency 150~300spm, even load 220~240spm, odd load 210~230spm |
Supply voltage | Three-phase 380V/50Hz. Voltage fluctuation range ±10% |
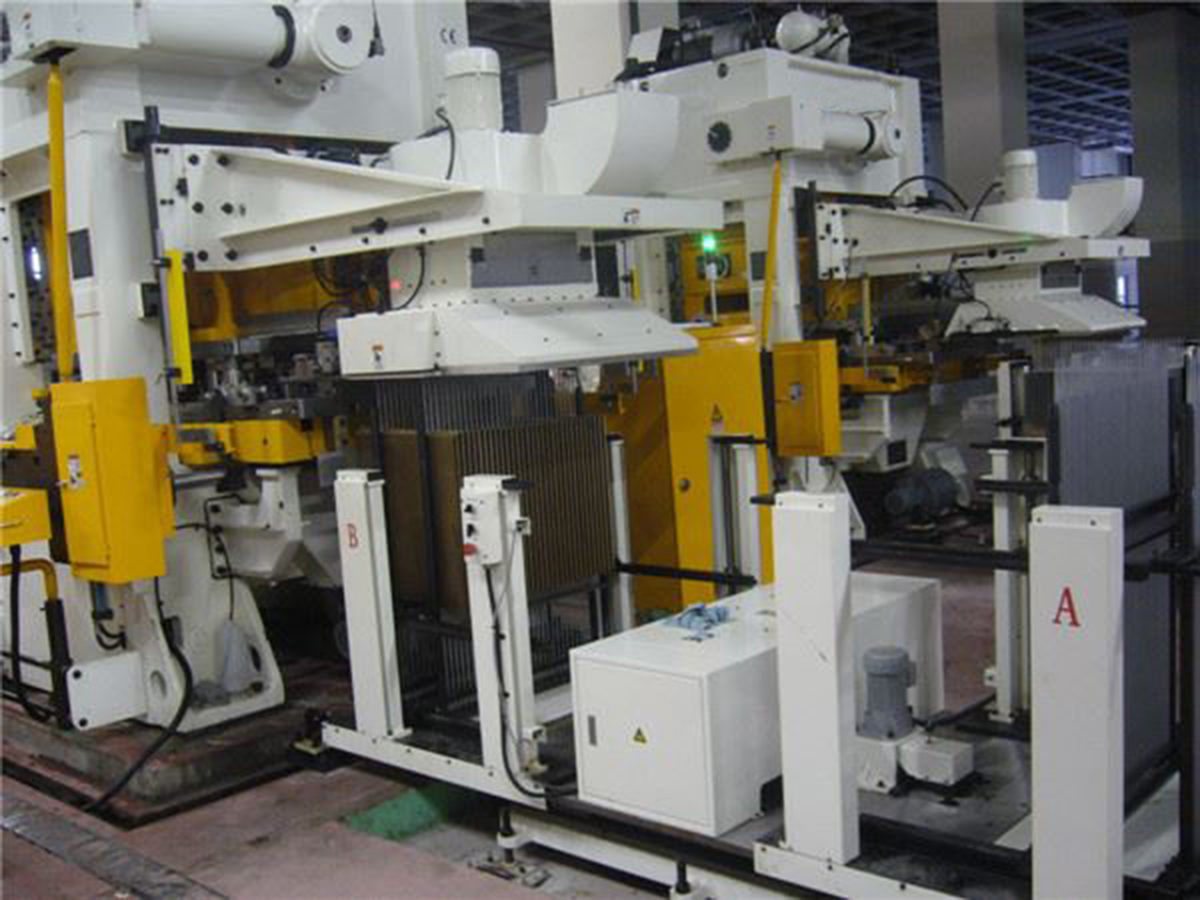
Main Technical Parameters Of The Production Line
Processing Material | Aluminum Foil |
The maximum diameter of coil material | 1200mm |
Coil material diameter | φ150 ± 5mm |
Maximum material width | 820mm |
Fin Die Pattern | Φ15.88×24R×1P (33×38.1mm) |
One feed step and feed switch | 1P/2P |
Suction length: | 1000mm |
Suction type | single fan, automatic stripper plate type, with a stripper plate |
Fin stack heigh | Lifting type automatic aggregate, the height can reach: 600~900mm |
Fin stack mode | Double-position automatic 180° swing back structure with automatic lift function. The needle assembly of the aggregate is moved along the linear guide, and the position of the aggregate needle is determined by positioning the pin |
Unloading mode | damper open plate discharge |
waste discharge method | Use a fan to blow the waste out of the organization, with a 7m pipe and a waste box |
Discharge rack loading direction | The loading direction is opposite to that of the operation panel, ie it is loaded from left to right when viewed from the discharge rack to the host |
Discharge rack type | single-head up type, hand wheel up tight type |
Machine Tool Installation | The machine tool is the anchor bolt installation method. The client must make the basics. The seller provides ground drawings |
Spare Parts: See The Packing List
①Foundation Bolts / ②Expansion Bolts / ③Y Seal Ring UHP300 / ⑤Y Seal Ring UN050 / ⑥Manual Grease Adding Gun
Main Components List
1.Dual electromagnetic valve for clutch | made byMAC (USA) |
2.PLC controller | made by MITSUBISHI (model: FXZN-48MT and FXON-16EY) |
3.Frequency Converter | made by MITSUBISHI(FR-S540-3.7K-CH-R for fin-suckor’s motor) |
4.Main pneumatic valves | made by FESTO (Germany) or SMC(Japan) |
5.Main electrical components | made by Schneider |
6.Hydraulic pump | made in Taiwan |
7.Hydraulic valve | made by ATOS (Italy)or Taiwan |
8.Reducer for decoiler | made in Taiwan |
9.Bearing for feeder change unit | made by IKO (Japan) |
10.Encoder | made by MITSUBISHI (model: F2-720-RSV) |
11.Toucher interface | made by MITSUBISHI (model: GT1055-QSBD-C) |
12.Auto grease pump | made by IHI(Japan) |
13.Decoiling sensors | made by OMRON (series: E3JK) |
14.No material testing sensors | made by OMRON (series: E3JK) |
15.Change switch | made by Schneider |
16.AC Contactor | made by Schneider |
17.Main button switch | made by IDEC(Japan) |
18.Indicator light | made by IDEC(Japan) |
19.Breaker | made by ABB |
20.Output relay | made by Carro Gavazzi(Swiss) |
Write your message here and send it to us