Double Head Hydraulic Tube Bending Machine
Product Description
1. Overview
It is composed by the material guide frame, bending device, discharge device, mandrel device, electrical system, pneumatic system components. Action cycle is as below:
Manual fix length of straight pipe material in place → pipe clamping → spray oil mist and bending → mandrel exit → pipe clamp loose → discharge → discharge reset (while manual reclaim) → bending reset.
2. Material Guide Frame Device
2.1 Bending length ≥800mm in use of material guide frame device
2.2 Guide frame pin hole positioning, easy installation without adjustment.
2.3 The guide frame is adjustable to accommodate different sizes of elbows.
3. Bending Device
3.1 Driven by hydraulic cylinder, through the gear tooth transition mechanism for bending.
3.2 When bending, the oil mist lubrication function works, can extend the service life of bending mold while improving the quality of the elbow.
3.3 The overall bending mold seat integrated processing, high precision and high precision.
3.4 The support mould and clamping mold are controlled by pneumatic cylinder.
3.5 Bending mold, clamping mold, and the supporting mould are use of alloy steel alloy material by the overall quenching by the CNC equipment precision machining, anti-wear, high precision.
4. Discharge Device
4.1 Discharge by the servo control return pipe to achieve the discharging.
4.2 Simple structure, easy for operation.
5. Mandrel Device
5.1 The return mandrel is controlled by pneumatic cylinder.
5.2 The mandrel rod support plate is hinged and automatically separated when sliding.
5.3 The mandrel rod length can be adjusted for each.
6. Electrical System
6.1 Electrical box is built-in type, operating box is hang type.
6.2 Machine is controlled by PLC, man-machine interface, servo motor and related electrical components, easy and efficient operation.
7. Hydraulic System
7.1 Separated hydraulic station.
7.2 Hydraulic pressure: 6MPa(±10%)
8. Pneumatic System
1. Compressed air pressure: 0.6MPa(±10%)
2. Compressed air capacity: 0.4m3/min
Product Features
Purpose:
The equipment is used to open, straighten, chipless cut and bend coil copper pipe into set length U shape pipe which is also called hairpin pipe; mainly applied to the auto production of long U pipe in air-condition condensers and evaporators.
Features:
1.Stripper, frame move and bend by servo motor.
2.Driven by frequency conversion moto and feed by belts.
3.Cutter motor is driven by transducer, and the speed can be adjusted.
Technical Parameters
S.N | Item | Specification | Remark |
1 | Bender Specification | <9.52mm 4pipes, | |
>9.52mm, 3 Pipes | |||
2 | Tube Material | Soft Cooper Tube | Or Soft Aluminum Tube |
3 | Tube Diameter | According To Customer’s Requirement | Φ7-Φ16 |
4 | Tube Thickness | According To Customer’s Requirement | 0.3-0.8mm |
5 | Center Distance Of The Tube After Bending | According To Customer’s Requirement | ≤41 |
6 | Max. Bending Length | 2650mm | |
7 | Min. Bending Length | 150mm | |
8 | Processing Cycle | 15 S/Pcs ( The Work Piece 1 M Long) | Not Including The Manual Feeding Time |
11 | Power Voltage | AC380V/50HZ/3ph | Can Be Tailor Made |
Main Component
S.N | Content | Brand/Origin |
1 | PLC Controller | LG |
2 | Man-Machine Interface | KINCO |
3 | Servo Motor | KINCO |
4 | Pneumatic Solenoid Valve | Taiwan ALLGREAT |
5 | Pneumatic Cylinder | Taiwan ALLGREAT |
6 | Electrical Component | LG/IDEC |
7 | Bending Servo Motor, Reducer | Siemens |
8 | Discharge Servo Motor, Reducer | Shanghai |
Acceptance Standard
1.Accuracy After Bending The Tube
1.1 Bending parts no obvious concave, drums, wrinkles and other defects.
1.2 After bending, the length of the two nozzles tolerance ≤ ± 0.6mm (except straight pipe length error).
2. The Bending Machine Operation Is Normal, No Stagnation. Pneumatic System Without Leakage
3. Spares (Not Including The Spares Installed On The Machine)
3.1 Universal mandrel 4 pcs
3.2 Discharge pipe 4pcs
3.3 Relay KJ2S-CL-D24 2pcs
4. User Manual
4.1 Safety operation and notice
4.2 Maintenance Schedule
4.3 Electrical schematic diagram, pneumatic system diagram
5. Color
Machine color is sky blue, electric control box and some protective areas using other matching colors to ensure that the entire production line as a whole excellent results. (Can be customized according to customer requirements)
6. Delivery Time
30-45 days before delivery, the buyer should provide more than 80pcs pipe sample, shipped to the seller's factory. The sample after testing return back to the buyer with the equipment
7. Acceptance
Acceptance and inspection executed at the seller’s production site. Meet the requirements of this technical requirement till to produce qualified products.
After Sales Services
1. In the warranty period, spares are free of cost (except the user improper use)
2. After the expiry of the warranty, the seller supplies the spares at the cost price.
3. Work range division: the seller will be ship the qualified equipment to the buyer, the buyer is responsible for equipment unloading, put in place and the machine outside water, electricity, gas pipeline installation, the seller is responsible for the installation and commissioning, to train the operator the maintenance, principle of equipment, daily operations, common fault repair, safety precautions, daily maintenance and other aspects of knowledge.
4. Warranty: 14 months after B/L date or 12 months after shipment.
Picture Display
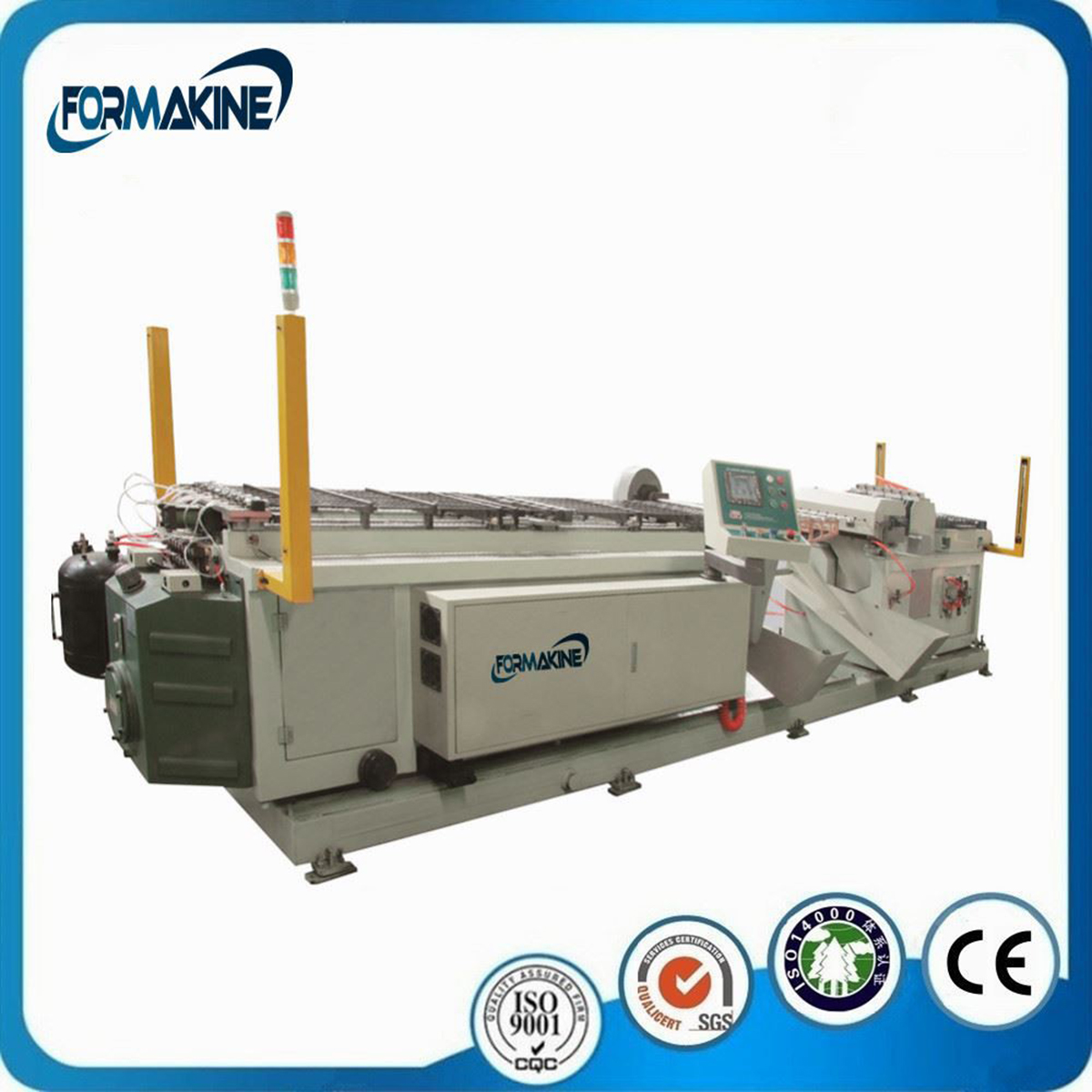
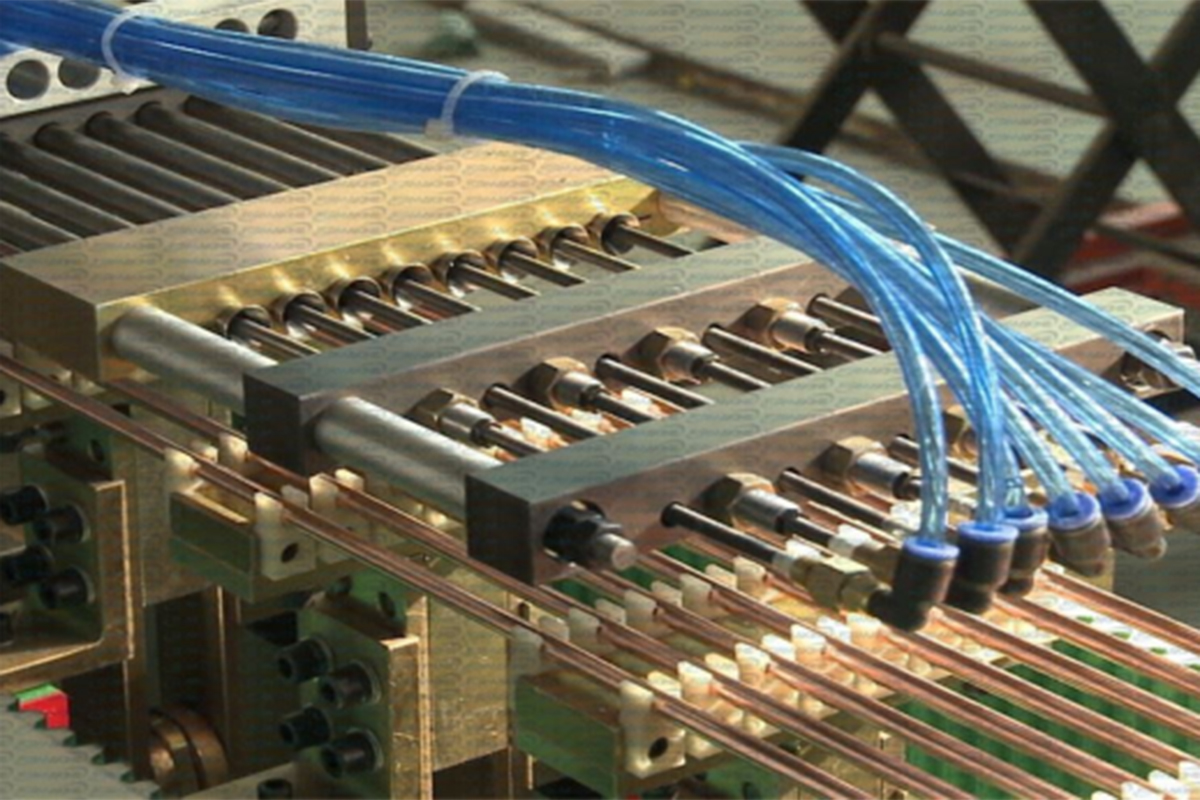
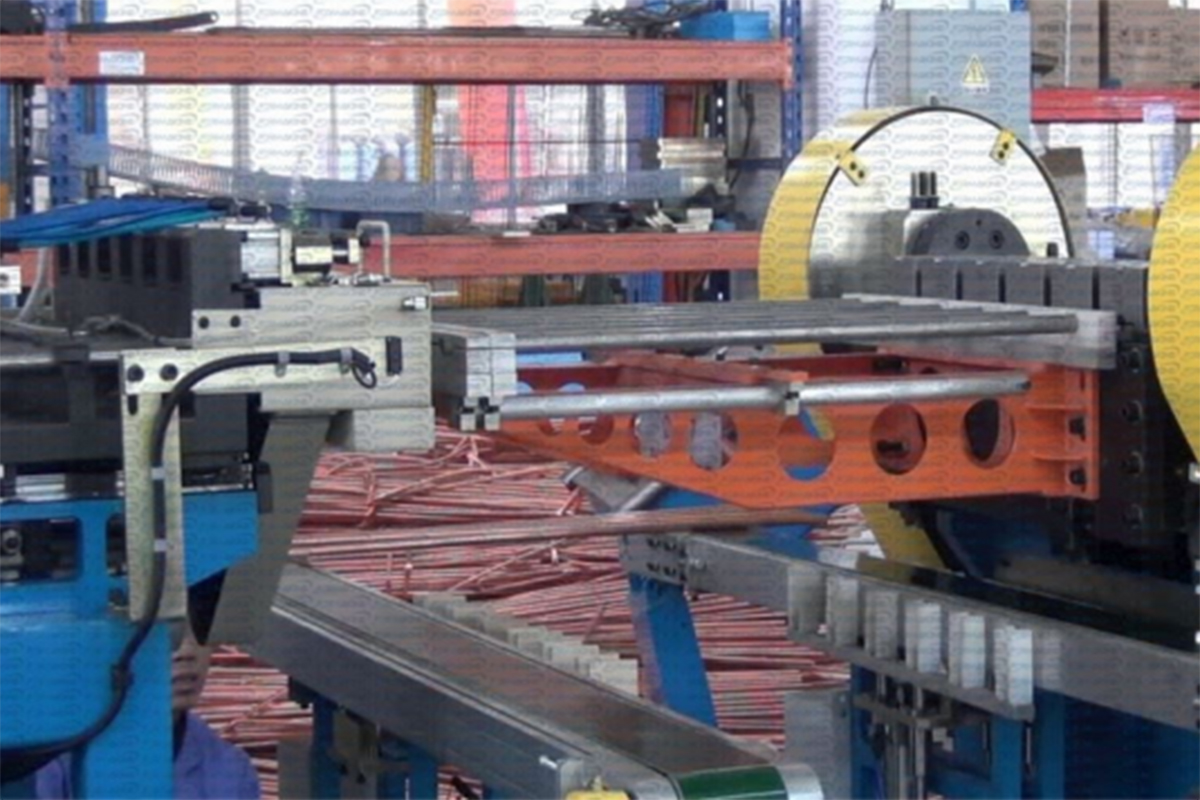
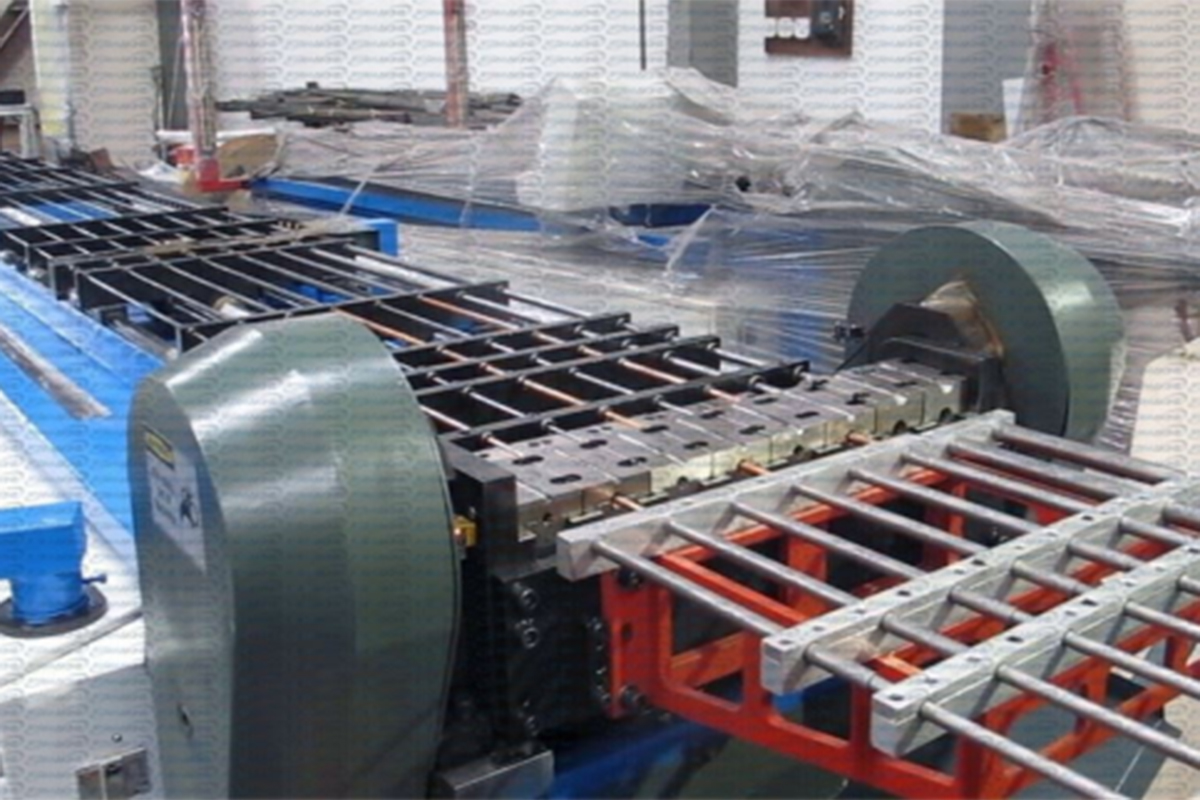
Option
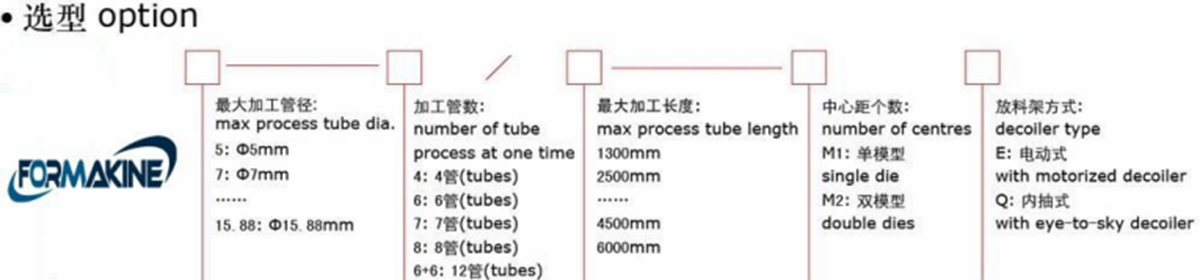
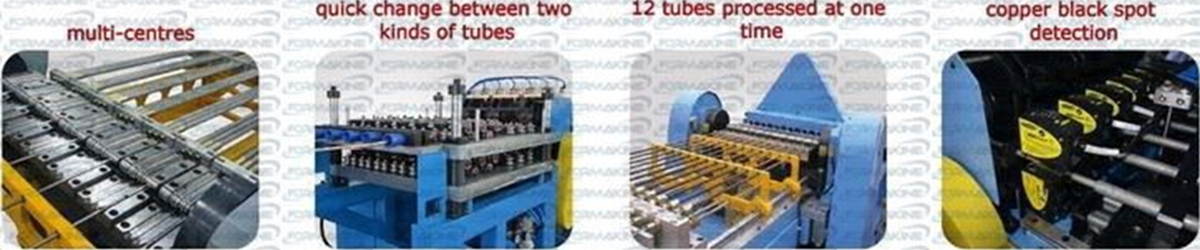
Machining Workshop
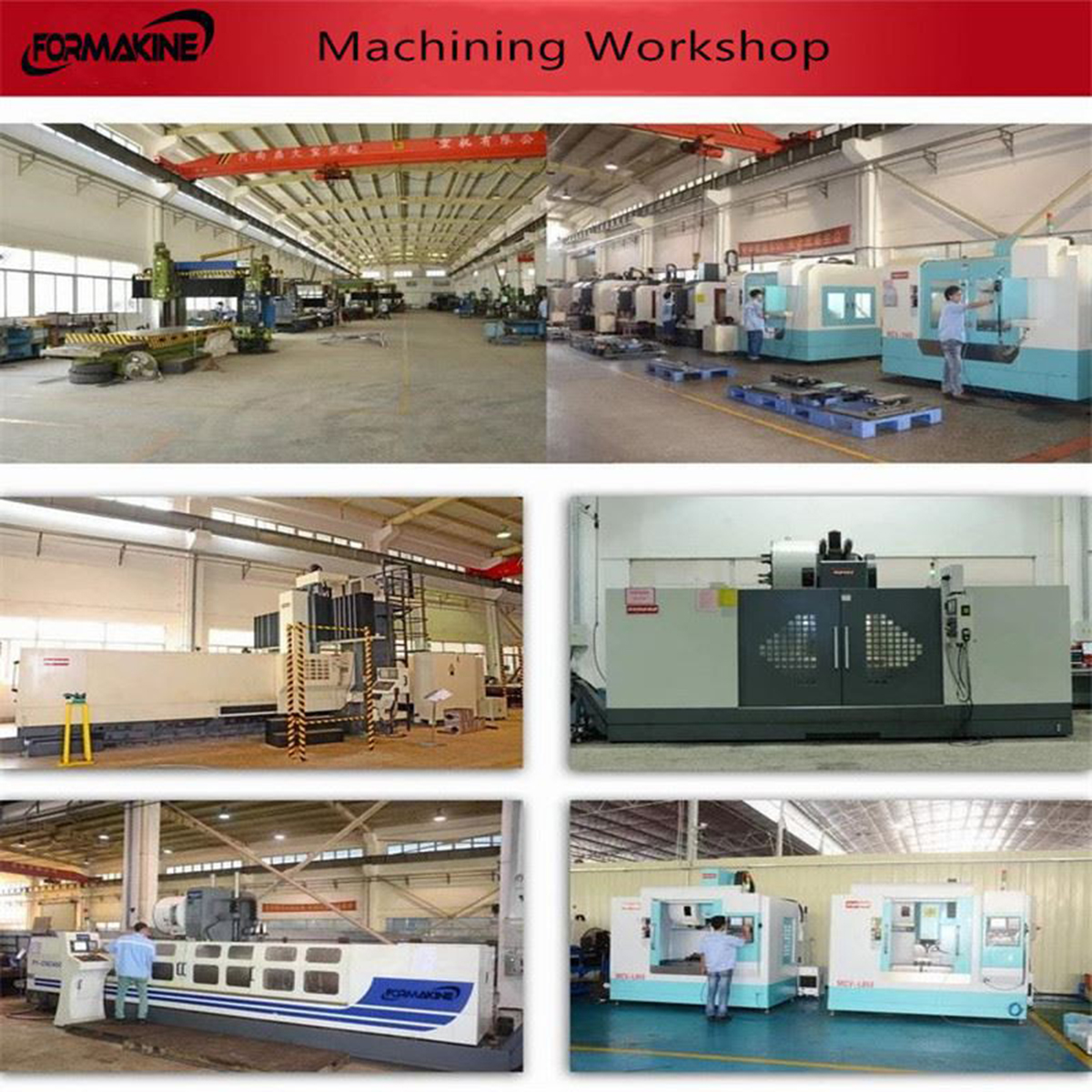
Assembly Workshop
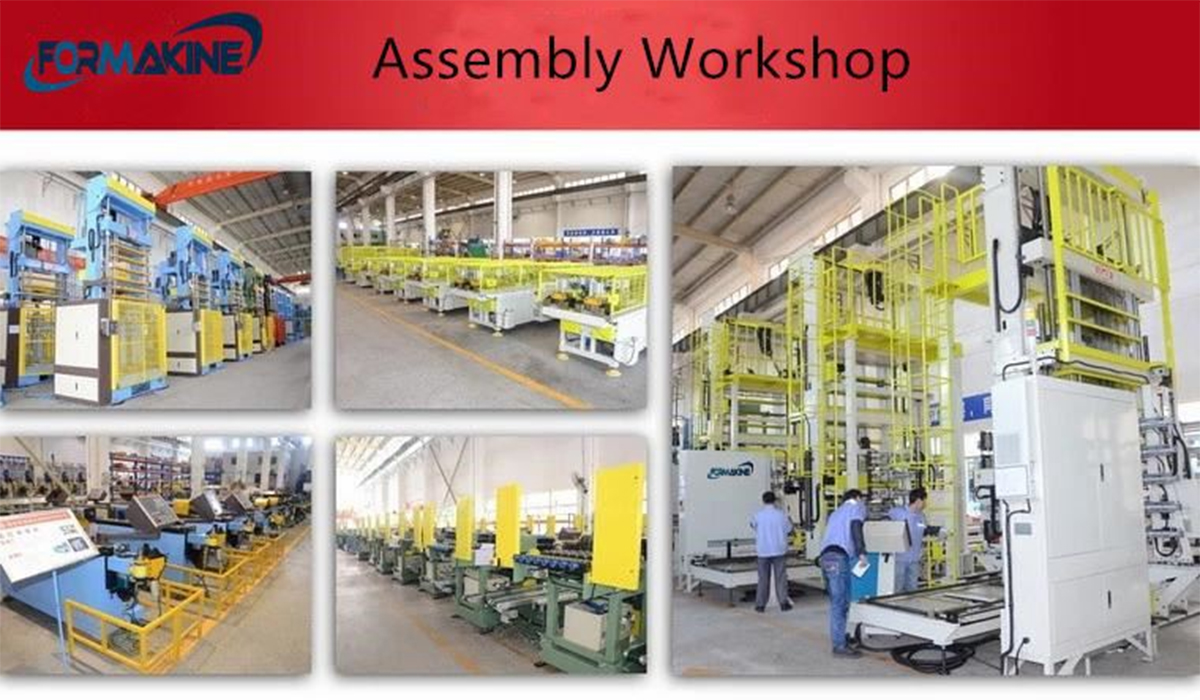
Detecting Device
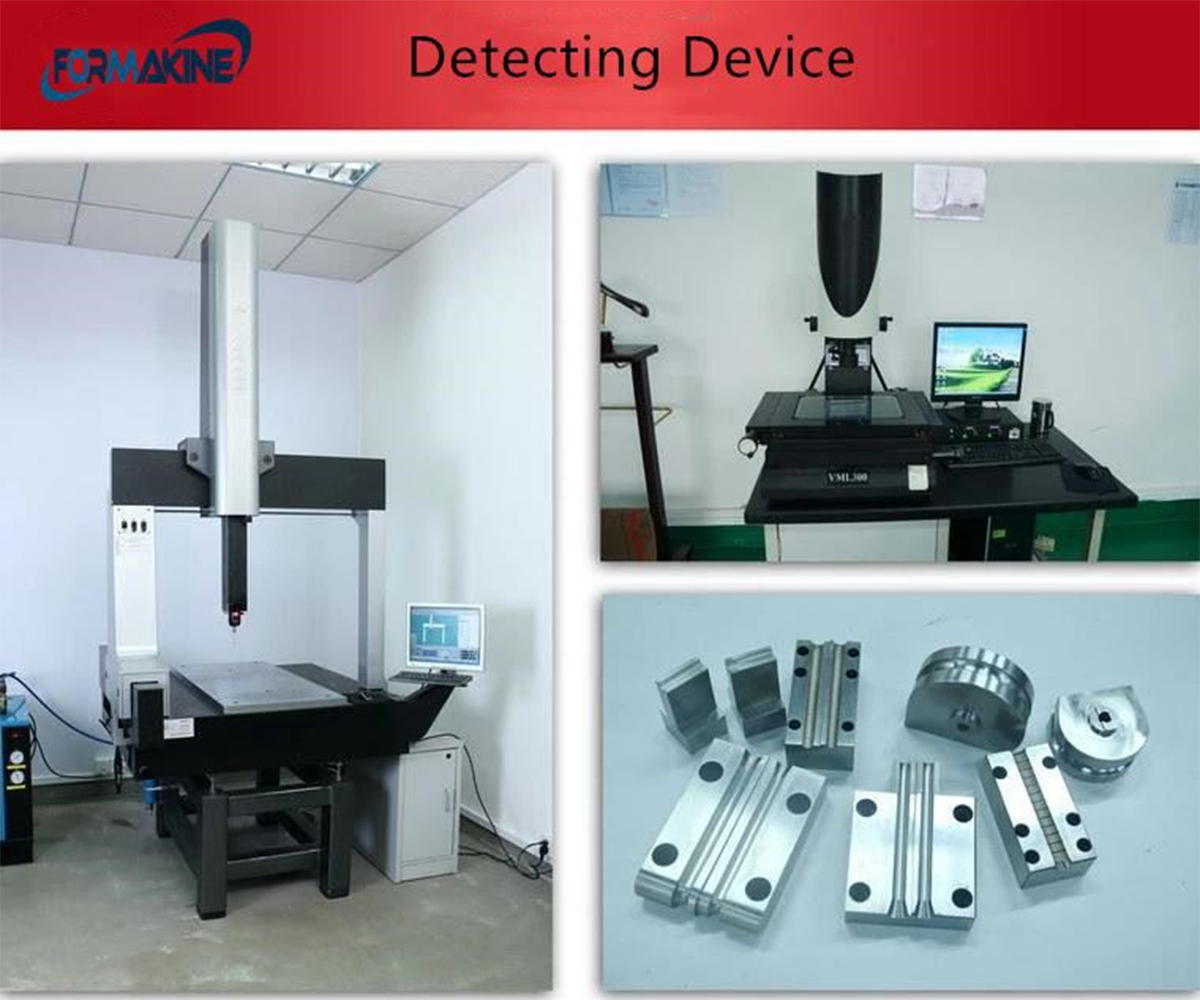